Anyone use 11.5 compression with forced induction?
#16
Try this link and search through it. Im too lazy to do it myself lol
http://my350z.com/forum/forced-induction-182/
http://my350z.com/forum/forced-induction-182/
#17
#18
I read that...sucks you had to go through that. People make mistakes I guess. Regardless, considering your car put down 400+whp on just 7psi was real nice...especially with the rod problem.
Last edited by GT-ER; 07-17-2009 at 10:45 PM.
#19
Thats what I mean... If it didn't have that 1 rod size issue, I'm sure I could of raised the boost maybe to 10 or 11lbs and put some serious power down. My car is at PF supercars now getting done. You should talk to Ray. He is a pro RX-7 tuner... if he can tune RX-7s to perfection, then he can tune our cars. Check their website out and give them a call.... he can answer a lot of questions. www.pfsupercars.com
Good luck!
Good luck!
#20
http://image.hotrod.com/f/editorials...nterprises.jpg
Is an extra 3% hp in the low end worth the risk of pre-detonation???
An LS2 is a 6.0L V8 and a VQ35 is a 3.5L V-6.
To get the same HP out of a VQ35, you need 33% more hp out of each cylinder, and each cylinder is 22.2% smaller. In other words, you need to cram 33% more air/fuel mixture into cylinders that are slightly over 3/4 the size of the LS2s.
You are going to need alot more boost to get 500 rwhp out of a VQ in comparision to an LS2, which means the VQ motor is going to be more prone to pre-detonation on 93 octane. In other words, to get 500 rwhp in a VQ35, you have to cram 71% more air/fuel per liter of displacement in comparison to an LS2.
Assuming the same compression ratio, that means the net pressure at TDC will be 71% higher in the VQ35 than in the LS2 to achieve the same HP. You are talking about going with 11.5:1 compression, so now your net pressure will 79% higher than the LS2 (ignoring cam phasing).
This might be OK if you are running race gas, but I would not recommend running that kind of compression on pump gas because you likely will get pre-detonation unless you pull the timing way, way back, which will more than offset the extra 3% hp gain you will get from the higher compression ratio.
Anyway, I'm just trying to help. It's your car and your money. Please post your results when you are done.
Last edited by TTG35forT; 07-20-2009 at 06:26 PM.
#21
You are correct that the rods are the weak point on a VQ35DE. But pre-detonation will become an issue if you raise the compression up to 11.5:1 and then boost the motor enough to get 500 rwhp (unless you plan on running race gas all of the time or a whole lot of meth injection).
Fact 1:
http://image.hotrod.com/f/editorials...nterprises.jpg
Is an extra 3% hp in the low end worth the risk of pre-detonation???
Fact 2:
An LS2 is a 6.0L V8 and a VQ35 is a 3.5L V-6.
To get the same HP out of a VQ35, you need 33% more hp out of each cylinder, and each cylinder is 22.2% smaller. In other words, you need to cram 33% more air/fuel mixture into cylinders that are slightly over 3/4 the size of the LS2s.
You are going to need alot more boost to get 500 rwhp out of a VQ in comparision to an LS2, which means the VQ motor is going to be more prone to pre-detonation on 93 octane. In other words, to get 500 rwhp in a VQ35, you have to cram 71% more air/fuel per liter of displacement in comparison to an LS2.
Assuming the same compression ratio, that means the net pressure at TDC will be 71% higher in the VQ35 than in the LS2 to achieve the same HP. You are talking about going with 11.5:1 compression, so now your net pressure will 79% higher than the LS2 (ignoring cam phasing).
This might be OK if you are running race gas, but I would not recommend running that kind of compression on pump gas because you likely will get pre-detonation unless you pull the timing way, way back, which will more than offset the extra 3% hp gain you will get from the higher compression ratio.
Anyway, I'm just trying to help. It's your car and your money. Please post your results when you are done.
Fact 1:
http://image.hotrod.com/f/editorials...nterprises.jpg
Is an extra 3% hp in the low end worth the risk of pre-detonation???
Fact 2:
An LS2 is a 6.0L V8 and a VQ35 is a 3.5L V-6.
To get the same HP out of a VQ35, you need 33% more hp out of each cylinder, and each cylinder is 22.2% smaller. In other words, you need to cram 33% more air/fuel mixture into cylinders that are slightly over 3/4 the size of the LS2s.
You are going to need alot more boost to get 500 rwhp out of a VQ in comparision to an LS2, which means the VQ motor is going to be more prone to pre-detonation on 93 octane. In other words, to get 500 rwhp in a VQ35, you have to cram 71% more air/fuel per liter of displacement in comparison to an LS2.
Assuming the same compression ratio, that means the net pressure at TDC will be 71% higher in the VQ35 than in the LS2 to achieve the same HP. You are talking about going with 11.5:1 compression, so now your net pressure will 79% higher than the LS2 (ignoring cam phasing).
This might be OK if you are running race gas, but I would not recommend running that kind of compression on pump gas because you likely will get pre-detonation unless you pull the timing way, way back, which will more than offset the extra 3% hp gain you will get from the higher compression ratio.
Anyway, I'm just trying to help. It's your car and your money. Please post your results when you are done.
Keep in mind the LS2 is also running stock bottom end ( which isn't exactly the strongest ) while I'd be running a forged bottom end. Maybe a better comparison is GTM's 600+whp VQ37VHR build...crazy stuff. Either way, maybe 11.5 is pushing it but I really don't see 11.0 being a problem. I also stated in my first post that race gas is not a problem. Maybe 400whp on pump and 500whp on race? Or maybe even stick to stock compression?
Interesting stuff no doubt...I just want the engine to be as peppy as possible off boost. With the mods I have now, I feel my engine is a DOG down low and I am worried it would only get worse.
BTW- pre-detonation = pre-ignition?

Last edited by GT-ER; 07-20-2009 at 07:51 PM.
#23
#24
I just finished building a new motor on my Z and we did go with 11.0 Pistons that were custom made from Arias. Initial road break in feels really nice and responsive, however I do plan on running an AEM Meth kit on pump gas 93octane for safety, and 116 octane for high boost...
I opted for the higher compression to wake up those APS extreme turbos, which seemed to feel dead until 4500 rpms especially with the Crower Stage 3 cams. With the higher compression, and overlap of the cams, it should be a perfect combination for the street and track.
I will post up the full details of the build once Im done doing break in and tune it.
I opted for the higher compression to wake up those APS extreme turbos, which seemed to feel dead until 4500 rpms especially with the Crower Stage 3 cams. With the higher compression, and overlap of the cams, it should be a perfect combination for the street and track.
I will post up the full details of the build once Im done doing break in and tune it.
#25


#26
Excellent post, and just the type of info I'm looking for ( though I wish someone would have already tried it before to have someone with actually experience ).
Keep in mind the LS2 is also running stock bottom end ( which isn't exactly the strongest ) while I'd be running a forged bottom end. Maybe a better comparison is GTM's 600+whp VQ37VHR build...crazy stuff. Either way, maybe 11.5 is pushing it but I really don't see 11.0 being a problem. I also stated in my first post that race gas is not a problem. Maybe 400whp on pump and 500whp on race? Or maybe even stick to stock compression?
Interesting stuff no doubt...I just want the engine to be as peppy as possible off boost. With the mods I have now, I feel my engine is a DOG down low and I am worried it would only get worse.
BTW- pre-detonation = pre-ignition?
Keep in mind the LS2 is also running stock bottom end ( which isn't exactly the strongest ) while I'd be running a forged bottom end. Maybe a better comparison is GTM's 600+whp VQ37VHR build...crazy stuff. Either way, maybe 11.5 is pushing it but I really don't see 11.0 being a problem. I also stated in my first post that race gas is not a problem. Maybe 400whp on pump and 500whp on race? Or maybe even stick to stock compression?
Interesting stuff no doubt...I just want the engine to be as peppy as possible off boost. With the mods I have now, I feel my engine is a DOG down low and I am worried it would only get worse.
BTW- pre-detonation = pre-ignition?

In other words, for the LS2/VQ35 example, let V1 be the volume of the air/fuel mixture in a cylinder at TDC in the LS2, and V2 be the volume of the air/fuel mixture in a VQ35 cylinder at TDC. T1 and T2 are the respective temperatures, and P1 and P2 are the respective pressures.
The pressure ratio P2/P1=(V1/V2)*(T2/T1)
If T1=T2, then P2/P1 = V1/V2 (which is what I assumed in the original post). However, T2 > T1, and not by an insignificant amount. Thus, to acheive 500 rwhp in an 11.5:1 CR VQ35, the pressure of the air/fuel misture at TDC will probably be more than double the pressure in an LS2 putting out the same hp. Thus, the octane requirements for the VQ35 will be higher than for the LS2. How much higher, I don't know, but I'm sure a little research will shed some light on the subject.
Last edited by TTG35forT; 07-22-2009 at 03:27 AM.
#27
I came across the following thread and found it very informative:
http://www.modularfords.com/forums/s...ad.php?t=51059
For anyone interested in the subject of compression ratio for boosted motors, I highly recommend reading the thread at the above link.
http://www.modularfords.com/forums/s...ad.php?t=51059
For anyone interested in the subject of compression ratio for boosted motors, I highly recommend reading the thread at the above link.
Last edited by TTG35forT; 07-22-2009 at 03:47 AM.
#29
Registered User
iTrader: (10)
Some more info for you I quote..
This article details some of the problems associated with trying to squeeze too much power out of a turbocharged engine and the common mistakes made by many people. Suggested reading of three other related articles on this site as a foundation for this article:
Ignition Tuning Ideas for Turbos
Ignition and Combustion
Fuel Octane vs. Horsepower
Intelligent Engine Modifications
Detonation
Detonation is defined as a form of combustion which involves too rapid a rate of energy release which produces excessive pressues and temperatures in the combustion chambers. These high pressures and temperatures can damage or destroy engine parts in short order. Detonation is often accompanied by an audible rattling sound.
Pre-ignition
Pre-ignition is defined as a normal combustion process starting before the ignition spark is initiated. This is usually caused by a local hot spot raising the mixture temperature above its auto ignition point. As combustion has started before it was intended to, peak cylinder pressure occurs too early in the cycle. This leads to excessive pressures and temperatures, often while the piston is still in an upwards motion with cylinder volume decreasing rather than increasing. Pre-ignition effects can include piston and spark plug electrode damage. Pre-ignition is usually not audible and can often lead to detonation.
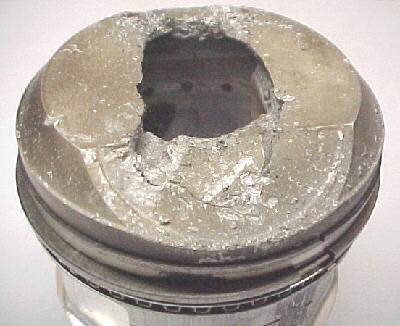
Effects of combined pre-ignition/ detonation event on piston dome
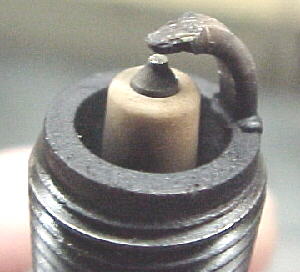
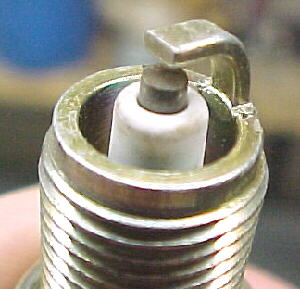
Plug suffering from mild pre-ignition damage left, normal plug right
Brake Mean Effective Pressure/ Peak Cylinder Pressures
BMEP is defined as the average effective combustion pressure occuring in a cycle. It can be calculated by using the formula:
792,000 X BHP divided by (engine displacement in cubic inches X RPM).
This figure is useful in comparing different engines operating on different fuels and the highest figure occurs at torque peak. The average range for engines is 200 to 400 psi.
Peak cylinder pressure (PCP)is the maximum chamber pressure achieved during the combustion process. This figure would normally be in the 600 to 2000 psi range.
Thermal Efficiency
Thermal efficiency describes the amount of energy extracted to perform useful work from the total energy contained in the fuel. TE is primarily affected by the compression ratio and ignition advance in a given engine design. Most engines are in the range of 25 to 35%. The lower the TE, the higher the exhaust gas temperature. TE can be caculated with the following formula:
2545 X BHP divided by (Btu/lb X lb. fuel/hr).
Specific Power Output
This describes the amount of hp developed per unit displacement. It is usually expressed in HP/liter or HP/cubic inch. This is useful in comparing different engines and stress limits. Generally speaking, the higher the specific output, the higher the stresses on the engine and the lower the engine life will be. It can be calculated by:
HP divided by engine displacement
Performance Considerations and Tuning Effects
On a given fuel, the maximum and mean cylinder pressures that can be achieved are limited to a certain figure. This is known as the knock limit. Trying to achieve cylinder pressures above the knock limit WILL destroy the engine. At wide open throttle, cylinder pressures can be altered by changing boost pressure and ignition timing. If the knock limit on a given fuel occurs at 700 psi PCP, this limit could be achieved by using 5 psi of boost with the timing set at 30 degrees BTDC or at 12 psi with the timing at 15 degrees BTDC. The engine will be considerably more efficient running less boost and more timing and the thermal stresses will be reduced as well.
As mentioned above, TE is affected by CR and ignition timing. As the timing is retarded, PCP is developed later in the cycle. This allows more energy to be lost through conduction into the water jackets because the piston is further down the bore and the rod has a less advantageous angle on the crank pin to deliver force to the crankshaft. Retarded timing also raises the exhaust gas temperature considerably. This raises the thermal stress on the pistons, spark plugs, valves, exhaust system and turbocharger. In severe cases of retarded timing, the mixture is still burning when the exhaust valve opens. Because turbochargers are driven by the energy in the exhaust stream, high EGTs caused by retarded timing produce so much energy at the turbine that even a fully open wastegate cannot control the boost pressure. All in all, retarded timing is counterproductive to producing an efficient, durable, powerful engine.
Most naturally aspirated engines require between 30 and 38 degress of ignition advance to achieve PCP at the correct crank pin position to make maximum power. By compressing the mixture through turbocharging, the rate of flame front progression increases and slightly less ignition advance is required to achieve PCP at the correct moment. In most cases, less than 5 degrees of retard is required however. We see many people throwing in 15 to 25 degrees of retard in a vain attempt to stop detonation at very high boost pressures for the fuel and compression ratios that they are running. It should be stressed that there are no free rides here. If you plan to achieve high specific outputs on low octane pump fuels for extended periods, you WILL have to reduce the CR. Truly high specific outputs are only available when using high octane fuels or by injecting anti-detonants. There are sound scientific reasons why there are no factory 10 to 1 CR turbocharged engines which produce specific outputs of 175 hp/L. In fact, there is NO production, piston, automotive engine which I am aware of which can achieve a specific output of this level on 92 octane pump fuel anywhere. Despite this fact, many people try to do this with expensive results. High compression ratios and high boost simply don't mix on pump fuel. If you try this, you will either be unhappy with the results or blow up the engine. When I say production engine, I mean one that you can buy off the showroom floor, no modifications, with the factory warranty intact. HP to be tested on a proper engine dyno, not on a chassis dyno with phantom flywheel correction factors applied. If Toyota, Honda or Ford could do this with factory reliability, don't you think that they would? As discussed in some of the reference articles above, set reasonable hp goals and modify the internal components as required to obtain these levels reliably. Be aware that many Japanese spec engines are designed to run on 98-102 octane fuel in their home markets. These engines will not be able to run the same boost levels on North American 92 octane fuel. Expect lots of detonation or spark retard if you attempt this.
This article details some of the problems associated with trying to squeeze too much power out of a turbocharged engine and the common mistakes made by many people. Suggested reading of three other related articles on this site as a foundation for this article:
Ignition Tuning Ideas for Turbos
Ignition and Combustion
Fuel Octane vs. Horsepower
Intelligent Engine Modifications
Detonation
Detonation is defined as a form of combustion which involves too rapid a rate of energy release which produces excessive pressues and temperatures in the combustion chambers. These high pressures and temperatures can damage or destroy engine parts in short order. Detonation is often accompanied by an audible rattling sound.
Pre-ignition
Pre-ignition is defined as a normal combustion process starting before the ignition spark is initiated. This is usually caused by a local hot spot raising the mixture temperature above its auto ignition point. As combustion has started before it was intended to, peak cylinder pressure occurs too early in the cycle. This leads to excessive pressures and temperatures, often while the piston is still in an upwards motion with cylinder volume decreasing rather than increasing. Pre-ignition effects can include piston and spark plug electrode damage. Pre-ignition is usually not audible and can often lead to detonation.
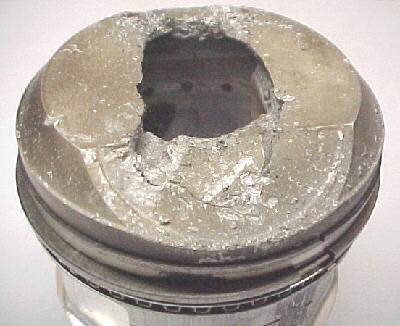
Effects of combined pre-ignition/ detonation event on piston dome
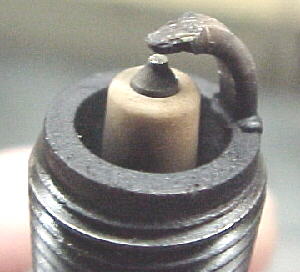
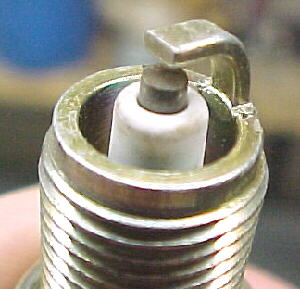
Plug suffering from mild pre-ignition damage left, normal plug right
Brake Mean Effective Pressure/ Peak Cylinder Pressures
BMEP is defined as the average effective combustion pressure occuring in a cycle. It can be calculated by using the formula:
792,000 X BHP divided by (engine displacement in cubic inches X RPM).
This figure is useful in comparing different engines operating on different fuels and the highest figure occurs at torque peak. The average range for engines is 200 to 400 psi.
Peak cylinder pressure (PCP)is the maximum chamber pressure achieved during the combustion process. This figure would normally be in the 600 to 2000 psi range.
Thermal Efficiency
Thermal efficiency describes the amount of energy extracted to perform useful work from the total energy contained in the fuel. TE is primarily affected by the compression ratio and ignition advance in a given engine design. Most engines are in the range of 25 to 35%. The lower the TE, the higher the exhaust gas temperature. TE can be caculated with the following formula:
2545 X BHP divided by (Btu/lb X lb. fuel/hr).
Specific Power Output
This describes the amount of hp developed per unit displacement. It is usually expressed in HP/liter or HP/cubic inch. This is useful in comparing different engines and stress limits. Generally speaking, the higher the specific output, the higher the stresses on the engine and the lower the engine life will be. It can be calculated by:
HP divided by engine displacement
Performance Considerations and Tuning Effects
On a given fuel, the maximum and mean cylinder pressures that can be achieved are limited to a certain figure. This is known as the knock limit. Trying to achieve cylinder pressures above the knock limit WILL destroy the engine. At wide open throttle, cylinder pressures can be altered by changing boost pressure and ignition timing. If the knock limit on a given fuel occurs at 700 psi PCP, this limit could be achieved by using 5 psi of boost with the timing set at 30 degrees BTDC or at 12 psi with the timing at 15 degrees BTDC. The engine will be considerably more efficient running less boost and more timing and the thermal stresses will be reduced as well.
As mentioned above, TE is affected by CR and ignition timing. As the timing is retarded, PCP is developed later in the cycle. This allows more energy to be lost through conduction into the water jackets because the piston is further down the bore and the rod has a less advantageous angle on the crank pin to deliver force to the crankshaft. Retarded timing also raises the exhaust gas temperature considerably. This raises the thermal stress on the pistons, spark plugs, valves, exhaust system and turbocharger. In severe cases of retarded timing, the mixture is still burning when the exhaust valve opens. Because turbochargers are driven by the energy in the exhaust stream, high EGTs caused by retarded timing produce so much energy at the turbine that even a fully open wastegate cannot control the boost pressure. All in all, retarded timing is counterproductive to producing an efficient, durable, powerful engine.
Most naturally aspirated engines require between 30 and 38 degress of ignition advance to achieve PCP at the correct crank pin position to make maximum power. By compressing the mixture through turbocharging, the rate of flame front progression increases and slightly less ignition advance is required to achieve PCP at the correct moment. In most cases, less than 5 degrees of retard is required however. We see many people throwing in 15 to 25 degrees of retard in a vain attempt to stop detonation at very high boost pressures for the fuel and compression ratios that they are running. It should be stressed that there are no free rides here. If you plan to achieve high specific outputs on low octane pump fuels for extended periods, you WILL have to reduce the CR. Truly high specific outputs are only available when using high octane fuels or by injecting anti-detonants. There are sound scientific reasons why there are no factory 10 to 1 CR turbocharged engines which produce specific outputs of 175 hp/L. In fact, there is NO production, piston, automotive engine which I am aware of which can achieve a specific output of this level on 92 octane pump fuel anywhere. Despite this fact, many people try to do this with expensive results. High compression ratios and high boost simply don't mix on pump fuel. If you try this, you will either be unhappy with the results or blow up the engine. When I say production engine, I mean one that you can buy off the showroom floor, no modifications, with the factory warranty intact. HP to be tested on a proper engine dyno, not on a chassis dyno with phantom flywheel correction factors applied. If Toyota, Honda or Ford could do this with factory reliability, don't you think that they would? As discussed in some of the reference articles above, set reasonable hp goals and modify the internal components as required to obtain these levels reliably. Be aware that many Japanese spec engines are designed to run on 98-102 octane fuel in their home markets. These engines will not be able to run the same boost levels on North American 92 octane fuel. Expect lots of detonation or spark retard if you attempt this.
#30
Registered User
iTrader: (10)
Making it Live
Reducing the compression ratio or using higher octane fuel are the two best ways to increase power on a turbocharged engine. If you drive on the street, you pretty well have to use pump fuel. In this case, you may want to fit some lower compression pistons. Pistons and spark plugs are often the first parts in the engine to suffer from the effects of overpressure and over temperature conditions. A high output engine should always be fitted with colder spark plugs- a point often overlooked by amateur engine builders. Forged pistons and turbo motors go together like jam and toast but there are wide variations between forged pistons. On a turbocharged application, temperatures and pressures will far exceed anything seen on a naturally aspirated engine. Because the specific output is higher, the rate of energy release is higher. Piston dome temperatures can run between 450 and 550 degrees F. Most aluminum alloys have lost over half of their strength at 400F. Turbo pistons need to have thick upper sections to be able to dissipate heat faster to the skirts and cylinder walls to keep dome temperatures down to safe limits. High silicon pistons can be fitted tighter because of their lower expansion rates for less rattling when cold but because they are more brittle, they don't stand as much detonation as a low silicon piston. Compression ratios for street use should generally be kept in the 7.0 to 8.5 to 1 range.
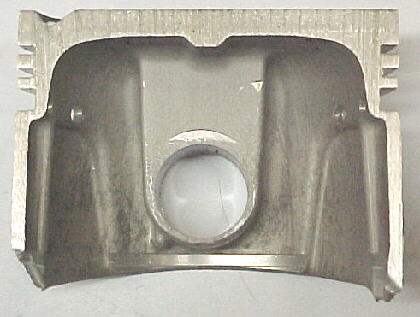
High silicon forged piston for use on naturally aspirated and low output turbocharging. Note relatively thin dome and corner radii.
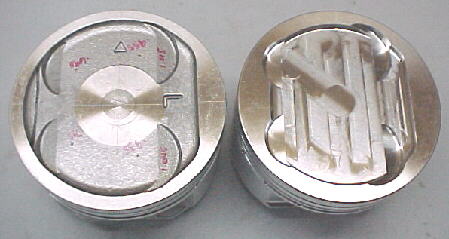
Cast factory piston left, custom designed low silicon, forged piston right
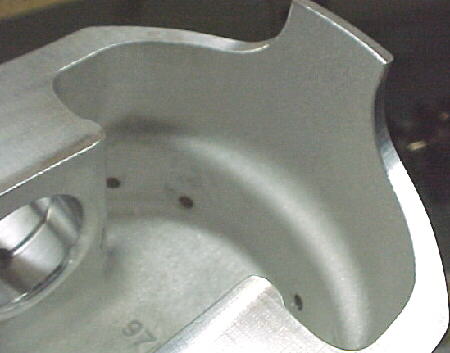
Note thick corner radii for higher heat tranfer rates
Most factory turbocharged engines are equipped with under- piston oil jets. These are an especially good idea on engines with large bores where the center of the piston dome is a long way away from the sides to be able to dissipate heat efficiently and extra thickness can add excessive weight to the reciprocating assembly.
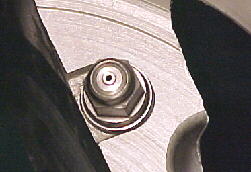
Oil jets
10/3/02 At Racetech, we get phone calls and E-mails every day from people wanting to make absurd hp figures on pump fuel on engines and drivetrains which are essentially stock. We're not trying to discourage you from your dreams, just trying to add a dose of reality. Assuming you get everything right and a 2L engine makes 400hp (unlikely), what drivetrain will transmit this power reliably to the ground, especially in a drag racing environment? The drag strips are littered with cars suffering from obliterated drivetrain parts being loaded onto flat beds at the end of race day. What is the point of this hp if something blows up every 5th pass? Build everything right to take your intended power. If you think your factory drivetrain will handle double or triple or quadruple the stock torque, you are in for an expensive surprise.
04/09/03 We talk to thousands of people every year with regards to EFI systems and modified engines. We get many people who just have to build a high compression turbocharged street engine. Even though we strongly suggest lowering the compression ratio, many people insist on 9 to 10 to 1 CRs. Usually these people phone back with sob stories of lots of pinging, blown head gaskets, melted plugs and pistons. We dispense free information based on 25 years of performance engine building experience to help people save money and disappointment. We frankly see very few high compression turbo engines running on pump fuel lasting more than a month before they fail. This is why you don't see any high power factory turbo cars with 10 to 1 CRs. Stick to under 8.5 Crs and you will make more power and have higher reliability.
Reducing the compression ratio or using higher octane fuel are the two best ways to increase power on a turbocharged engine. If you drive on the street, you pretty well have to use pump fuel. In this case, you may want to fit some lower compression pistons. Pistons and spark plugs are often the first parts in the engine to suffer from the effects of overpressure and over temperature conditions. A high output engine should always be fitted with colder spark plugs- a point often overlooked by amateur engine builders. Forged pistons and turbo motors go together like jam and toast but there are wide variations between forged pistons. On a turbocharged application, temperatures and pressures will far exceed anything seen on a naturally aspirated engine. Because the specific output is higher, the rate of energy release is higher. Piston dome temperatures can run between 450 and 550 degrees F. Most aluminum alloys have lost over half of their strength at 400F. Turbo pistons need to have thick upper sections to be able to dissipate heat faster to the skirts and cylinder walls to keep dome temperatures down to safe limits. High silicon pistons can be fitted tighter because of their lower expansion rates for less rattling when cold but because they are more brittle, they don't stand as much detonation as a low silicon piston. Compression ratios for street use should generally be kept in the 7.0 to 8.5 to 1 range.
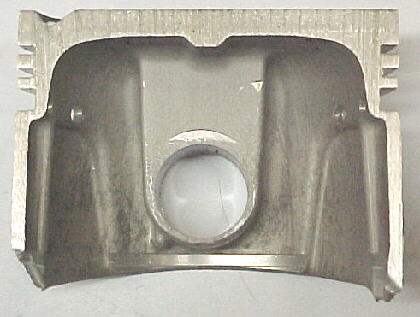
High silicon forged piston for use on naturally aspirated and low output turbocharging. Note relatively thin dome and corner radii.
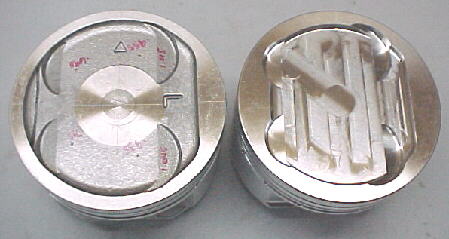
Cast factory piston left, custom designed low silicon, forged piston right
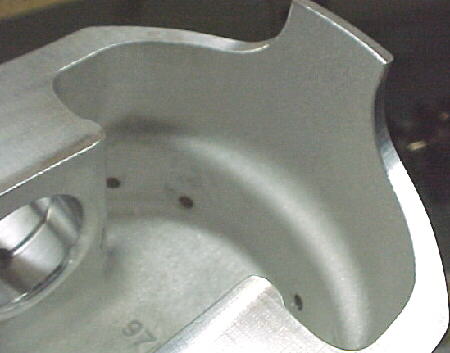
Note thick corner radii for higher heat tranfer rates
Most factory turbocharged engines are equipped with under- piston oil jets. These are an especially good idea on engines with large bores where the center of the piston dome is a long way away from the sides to be able to dissipate heat efficiently and extra thickness can add excessive weight to the reciprocating assembly.
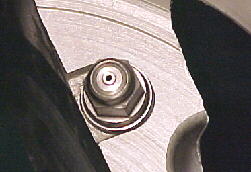
Oil jets
10/3/02 At Racetech, we get phone calls and E-mails every day from people wanting to make absurd hp figures on pump fuel on engines and drivetrains which are essentially stock. We're not trying to discourage you from your dreams, just trying to add a dose of reality. Assuming you get everything right and a 2L engine makes 400hp (unlikely), what drivetrain will transmit this power reliably to the ground, especially in a drag racing environment? The drag strips are littered with cars suffering from obliterated drivetrain parts being loaded onto flat beds at the end of race day. What is the point of this hp if something blows up every 5th pass? Build everything right to take your intended power. If you think your factory drivetrain will handle double or triple or quadruple the stock torque, you are in for an expensive surprise.
04/09/03 We talk to thousands of people every year with regards to EFI systems and modified engines. We get many people who just have to build a high compression turbocharged street engine. Even though we strongly suggest lowering the compression ratio, many people insist on 9 to 10 to 1 CRs. Usually these people phone back with sob stories of lots of pinging, blown head gaskets, melted plugs and pistons. We dispense free information based on 25 years of performance engine building experience to help people save money and disappointment. We frankly see very few high compression turbo engines running on pump fuel lasting more than a month before they fail. This is why you don't see any high power factory turbo cars with 10 to 1 CRs. Stick to under 8.5 Crs and you will make more power and have higher reliability.